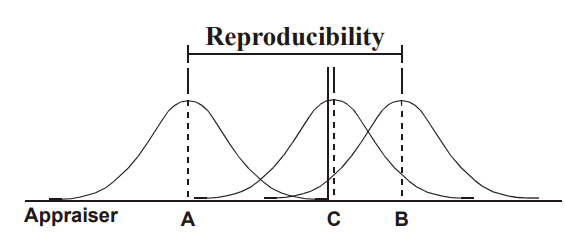
Precision
Width Variation, Traditionally, precision describes the net effect of discrimination, sensitivity and repeatability over the operating range (size, range and time) of the measurement system. In some organizations precision is used interchangeably with repeatability. In fact, precision is most often used to describe the expected variation of repeated measurements over the range of measurement; that range may be size or time (i.e., “a device is as precise at the low range as high range of measurement”, or “as precise today as yesterday”). One could say precision is to repeatability what linearity is to bias (although the first is random and the other systematic errors). The ASTM defines precision in a broader sense to include the variation from different readings, gages, people, labs or conditions.
Repeatability
This is traditionally referred to as the “within appraiser” variability. Repeatability is the variation in measurements obtained with one measurement instrument when used several times by one appraiser while measuring the identical characteristic on the same part. This is the inherent variation or capability of the equipment itself. Repeatability is commonly referred to as equipment variation (EV), although this is misleading. In fact, repeatability is the common cause (random error) variation from successive trials under defined conditions of measurement. The best term for repeatability is within system variation when the conditions of measurement are fixed and defined – fixed part, instrument, standard, method, operator, environment, and assumptions. In addition to within-equipment variation, repeatability will include all within variation (see below) from any condition in the error model.

Possible causes for poor repeatability include:
Within-part (sample): form, position, surface finish, taper, sample consistency
Within-instrument: repair; wear, equipment or fixture failure, poor quality or maintenance
Within-standard: quality, class, wear
Within-method: variation in setup, technique, zeroing, holding, clamping
Within-appraiser: technique, position, lack of experience, manipulation skill or training, feel, fatigue
Within-environment: short-cycle fluctuations in temperature, humidity, vibration, lighting, cleanliness
Violation of an assumption – stable, proper operation
Instrument design or method lacks robustness, poor uniformity
Wrong gage for the application
Distortion (gage or part), lack of rigidity
Application – part size, position, observation error (readability,parallax)
Reproducibility
This is traditionally referred to as the “between appraisers” variability. Reproducibility is typically defined as the variation in the average of the
measurements made by different appraisers using the same measuring instrument when measuring the identical characteristic on the same part.
This is often true for manual instruments influenced by the skill of the operator. It is not true, however, for measurement processes (i.e., automated systems) where the operator is not a major source of variation. For this reason, reproducibility is referred to as the average variation between systems or between-conditions of measurement
The ASTM definition goes beyond this to potentially include not only different appraisers but also different: gages, labs and environment(temperature, humidity) as well as including repeatability in the calculation of reproducibility.

Potential sources of reproducibility error include:
Between-parts (samples): average difference when measuring types of parts A, B, C, etc, using the same instrument, operators, and method.
Between-instruments: average difference using instruments A, B, C, etc., for the same parts, operators and environment. Note: in this study reproducibility error is often confounded with the method and/or operator.
Between-standards: average influence of different setting standards in the measurement process.
Between-methods: average difference caused by changing point densities, manual versus automated systems, zeroing, holding or clamping methods, etc.
Between-appraisers (operators): average difference between appraisers A, B, C, etc., caused by training, technique, skill and experience. This is the recommended study for product and process qualification and a manual measuring instrument.
Between-environment: average difference in measurements over time 1, 2, 3, etc. caused by environmental cycles; this is the most common
study for highly automated systems in product and process qualifications.
Violation of an assumption in the study
Instrument design or method lacks robustness
Operator training effectiveness
Application – part size, position, observation error (readability, parallax)
source of Width Variation: Analysis of measurement systems